Atlantic Packaging
Improved plant performance at Atlantic Packaging
Discover how Atlantic Packaging significantly improved overall plant performance, reducing late orders and improving processes by implementing CorrPlan.
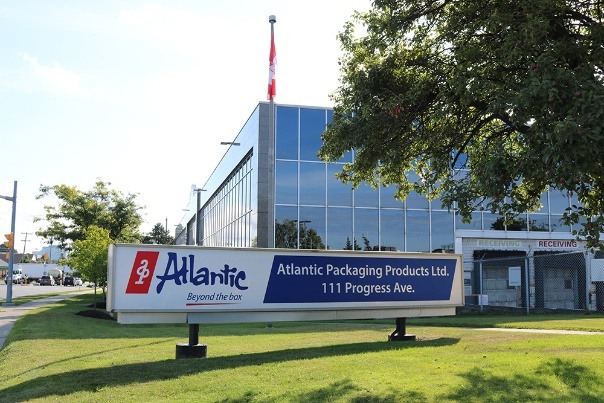
About the company
Atlantic Packaging Products Ltd., headquartered in Ontario, Canada, is a leading provider of innovative and sustainable packaging solutions.
Founded in 1945, the company specializes in corrugated and flexible packaging, recycled fiber, and container board. With over 25 manufacturing facilities and over 2,500 employees, Atlantic offers comprehensive packaging services, including design, inventory management, and recycling.
The challenge
The people of Atlantic Packaging know how to create high-quality corrugated packaging materials. For over sixty years, their commitment to service and quality led to the corrugated division becoming the leading manufacturer of corrugated packaging in the Toronto area, and one of the leading corrugated manufacturers in Canada.
Atlantic’s focus has always been on service and quality—doing things right, doing them fast, and delivering on time. Because of this commitment to service, Atlantic typically accepts any order from its customers, regardless of size and lead time. While this philosophy has helped Atlantic remain successful, its success has created another set of challenges that Atlantic needed to overcome in order to continue to thrive.
Manufacturers throughout North America have been challenged by the recent economic downturn, as has Atlantic’s corrugated division. “Customers are increasingly sensitive to price and service levels, and we’ve started to see increased competition from Canadian companies outside of Ontario, and from U.S. manufacturers,” said Mark Ragotte, Vice President of Manufacturing for Atlantic’s Corrugated Division.
This increasing sensitivity to service levels and cost, along with Atlantic’s high order volume, meant that Atlantic was being challenged to deal with shorter order lead times, deliver higher levels of service, and control manufacturing costs in the face of a global recession.
Fortunately, Atlantic’s commitment to continuous improvement meant they had a team and culture in place that could identify these challenges, suggest solutions, and successfully execute those plans. “One of the biggest issues we identified was a lack of sufficient capacity planning,” said Ragotte. “All orders were pushed through the plant and expedited. Plant managers were spending excessive time putting out fires when they could have been better utilized improving processes and product quality.” ”Poor visibility within our plants and schedules made addressing this difficult,” added Sean Crosbie, Manager of Atlantic’s Progress, Ontario plant.
Key challenges
The solution
To address these challenges and remain competitive, Atlantic recognized that it had to improve its existing processes and visibility throughout its plants, from order entry to shipping. The emphasis was on improved planning and scheduling—to achieve better plant capacity utilization and increased visibility throughout their manufacturing processes. Most importantly, Atlantic’s management and production personnel supported the project, demonstrating their company’s culture of continuous improvement.
“We didn’t have the right tools for the job and weren’t getting the job done... We looked at several solutions, and visibility—the full picture— led us to choose CorrPlan.” “We had to change processes—create focus on planning and scheduling,” says Hamid Meshkat, a supply chain consultant working for Atlantic.
One significant change Atlantic made was consolidating all planning and scheduling personnel and processes—including those in the shipping department—into a single planning group to facilitate constant communication between shipping and planning.
“We created a planning group to coordinate scheduling better, but we needed the right tools to give us the bigger picture throughout the plants,” says Meshkat. To find the right tools, Atlantic Packaging looked to eProductivity Software.
“CorrPlan was perfect for us as the primary tool to accommodate capacity planning... What took several minutes, or longer, on the old system now takes seconds with CorrPlan.”
CorrPlan is an automated, rule-based plant scheduling system that increases on-time deliveries and optimizes plant production for corrugated manufacturers. It allows planners to determine the most efficient and profitable manufacturing schedule possible based on user—selected rules tailored to their unique business processes and needs.
CorrPlan’s AutoPlan™ algorithms use capacity-constrained resource analysis and job sequencing rules unique to the plant, each work center, and— where required—to specific customers to generate schedules considering on-time delivery, plant throughput, and individual work center efficiencies.
Planners can review the schedule, make necessary changes, or test different scheduling scenarios. CorrPlan offers a breadth of functionality that enables manufacturers to improve planning, meet fluctuating customer demand, and collaborate internally across their manufacturing operations.
“CorrPlan was perfect for us as the primary tool to accommodate capacity planning,” says Crosbie, “What took several minutes, or longer, on the old system now takes seconds with CorrPlan.”
In addition to consolidating planning and adopting CorrPlan as the scheduling and capacity planning tool of choice, Atlantic also began transferring the knowledge of their plant-floor supervisors to the planning group. This enabled planners to better understand and respond to unique situations on the plant floor. This knowledge transfer also allowed planners to utilize better CorrPlan, which can be tailored to support each plant's unique processes and constraints.
“The eProductivity Software and Atlantic teams did a fabulous job on the implementation... Service levels have improved throughout the plant, we’ve improved trailer utilization in shipping, and product quality has improved.”
“CorrPlan gave us the ability to use and balance “push” and “pull” planning—the extremes of either method are no good,” says Ragotte. The consolidation of planning and the ability to balance push vs. pull scheduling allowed Atlantic to provide 24 hours-a-day planning coverage. This means the planning group can continuously adjust the balance of scheduled orders to optimize production flow through the plant—and maximize utilization of converting machines.
The result
Since implementing CorrPlan alongside its improved processes, Atlantic Packaging has realized a significant improvement in overall plant performance.
“The eProductivity Software and Atlantic teams did a fabulous job on the implementation,” says Ragotte. “Service levels have improved throughout the plant, we’ve improved trailer utilization in shipping, and product quality has improved. We removed the fire-fighting, and now our managers and supervisors can focus on quality and service.”
“Software is not a magic bullet,” says Ragotte. “Even with software, hiccups still happen, but CorrPlan can minimize the occurrence and impact of surprises, and has helped the Atlantic team cope with unexpected breakdowns and changes.”
When asked what he felt was the biggest benefit that Atlantic has realized since implementing CorrPlan, Ragotte replied “We’ve reduced problems [production bottlenecks and jam-ups] between the Corrugator and converting machines, and most importantly, we’ve seen a significant reduction in late orders. CorrPlan was integral to developing the right structures and processes to achieve these results.
"Service levels have improved throughout the plant, we’ve improved trailer utilization in shipping, and product quality has improved. We removed the fire-fighting, and now our managers and supervisors can focus on quality and service."
Hamid Meshkat,
Supply Chain Consultant, Atlantic Packaging