CorrBoard
Transforming the corrugator: Operational excellence at CorrBoard with Escada
Discover how CorrBoard leveraged ePS Escada to transform its operations, enhance efficiency, and solidify its commitment to sustainability.
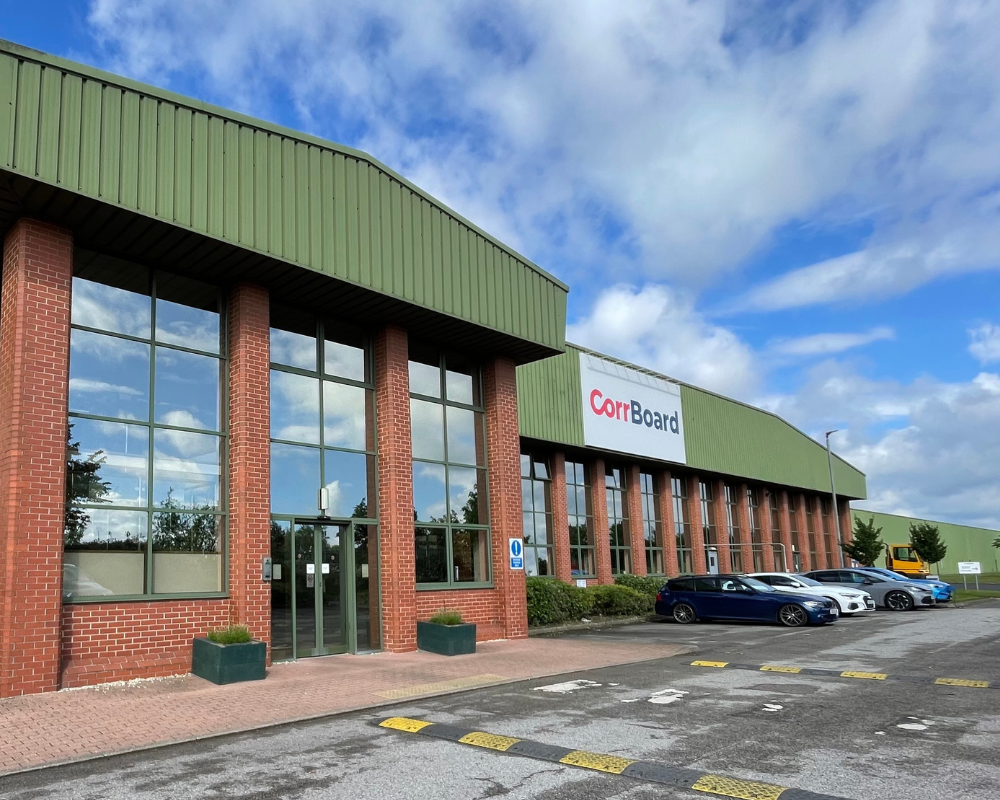
About the company
CorrBoard is an independent producer of corrugated board, prioritizing flexibility and reliability. The company has invested heavily in sustainable technology to provide corrugated packaging solutions for various industries.
Based in Scunthorpe, CorrBoard supplies corrugated board throughout the UK. Their independence enables investment in innovative, sustainable equipment tailored to diverse client needs. CorrBoard has collaborated with some of the most prominent leaders in the packaging industry. Its team is committed to becoming the UK's largest corrugated board supplier, focusing on sustainability and innovation.
The challenge
CorrBoard faced numerous challenges upon entering the industry. The complexity of manufacturing corrugated board requires a deep understanding of the systems that underpin the process.
The company's initial struggle was the lack of integration and communication among different Original Equipment Manufacturers (OEMs) involved in the manufacturing process.
Key requirements
Katie Woodward, Head of Operations at CorrBoard, explains: "When I first came into this industry, everyone said that making cardboard is black magic, but when you look into it, it boils down to the processes you have in place. You have the same raw materials going into a machine, and while the machine can have different components, controlling the corrugator is crucial to what comes out the other side.”
One of the first steps towards overcoming these challenges was establishing strong relationships with key OEMs. CorrBoard worked tirelessly to foster collaboration between OEMs, ensuring that issues could be addressed collectively rather than in isolated silos.
Katie adds: "One of the biggest challenges I faced with this role was managing the key OEMs involved in the corrugating hall. These OEMs are all intertwined, so issues in one section can affect the entire corrugator. Initially, we needed stronger relationships with these OEMs and often faced a blame game when problems arose."
The solution
Escada played a crucial role in CorrBoard's transformation by providing advanced corrugator process and quality control systems and expertise in optimizing machine settings. The relationship with Escada enabled CorrBoard to achieve greater flexibility, reduce waste, and enhance product quality.
Katie explains further: "Our team has done a tremendous amount of work with Escada. When raw materials enter the process, they are controlled by another OEM, but when it comes to changing the settings for different grades, each grade requires specific settings to ensure quality."
Escada's control systems allowed CorrBoard to adjust settings based on seasonal variations, ensuring consistent product quality throughout the year. By understanding and manipulating steam pressure settings for different board grades, CorrBoard could more effectively meet specific customer requirements.
Katie highlights the impact: "Manufacturing corrugated board depends on the seasons. In winter, your settings and control systems need to be different from those in summer because our product is not plastic; it's open to the elements and can change based on its surroundings."
Sustainability is a core focus for CorrBoard, with the company optimizing its processes to reduce waste and energy consumption. The collaboration with Escada allowed CorrBoard to switch to using locally sourced starch, further reducing its environmental footprint.
Katie shares insights on sustainability: "Sustainability goes right to the heart of our business. Waste has always been an operational target for us - something we can control to a degree. By using Escada to adjust settings like heat, pressure, and starch based on conditions such as humidity and temperature, we can significantly reduce waste and improve product quality."
The results
Since adopting Escada's solutions, CorrBoard has experienced significant growth and enhanced operational efficiency. The company heavily invested in its workforce, fostering a culture of continuous improvement and development. Low staff turnover rates and extensive training programs contributed to a motivated and skilled workforce capable of driving the company forward.
Katie emphasizes the importance of culture: "Since I started in this role, we have heavily invested in our culture, and it’s been a significant journey. We have a very low staff turnover and focus on training programs and talent development."
CorrBoard's commitment to transparency and customer communication has set it apart in the industry. By clearly presenting its capabilities and maintaining open lines of communication, CorrBoard has built solid and trust-based relationships with its clients.
Katie notes: "We want to work with anyone who wants to work with us. Sustainability, credibility, and communication are incredibly important to us. We may be unusual in the market because we over-communicate, but we believe it's vital for customers to know where their product is and if there are any issues."
The partnership between CorrBoard and Escada has been instrumental in transforming CorrBoard's operations. Through system optimization, sustainability initiatives, and a strong focus on culture and training, CorrBoard has positioned itself as a leader in the corrugated board manufacturing industry.
Katie concludes: "Our relationship with Escada has been crucial over the past few years. People often say it's who you know, not what you know, but in technology, it's a balance of both. The relationship with Escada has taught us a lot about customer service and support, setting us apart from our competitors."
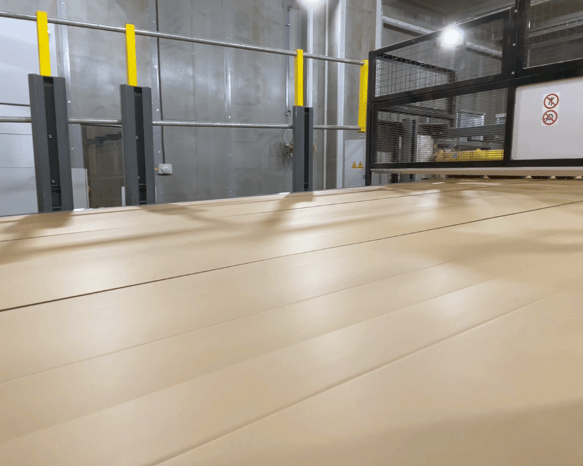
"Our relationship with Escada has been crucial over the past few years. People often say it's who you know, not what you know, but in technology, it's a balance of both. The relationship with Escada has taught us a lot about customer service and support, setting us apart from our competitors."
Katie Woodward
Head of Operations, CorrBoard