MES Applications
Is your Enterprise resource planning (ERP) lacking industry-specific functionality?
Explore MES software to unify your data, accelerate quoting, and optimize your manufacturing processes - whilst saving time and money.
Integrate with Ease
Achieve 90% integration readiness with a single effort - thanks to a common API.
Pre-built Functionality
Save time and money compared to custom or generic solutions.
Industry Specific
Backed by over 30 years of experience.
Fragmented data?
Transform fragmented or inaccessible data into actionable insights to drive better decision-making, enhance efficiency, and gain a clearer understanding of your packaging business operations.
BI delivers customized insights across all business levels with powerful real time data, intuitive interface, and interactive dashboards; driving data-driven decisions and continuous improvement through a seamless web-based platform.
%20analytics%20software.png?width=583&height=477&name=ePS%20Packaging%20-%20Business%20Intelligence%20(BI)%20analytics%20software.png)
Rigid, complex scheduling?
Simplify even the most complicated production schedules.
Minimize make-ready times to reduce switch-over costs, ensure efficient equipment usage, enhance capacity management, and minimize waste; using AI technology PrintFlow® 4D increases throughput, and minimizes manual touchpoints.
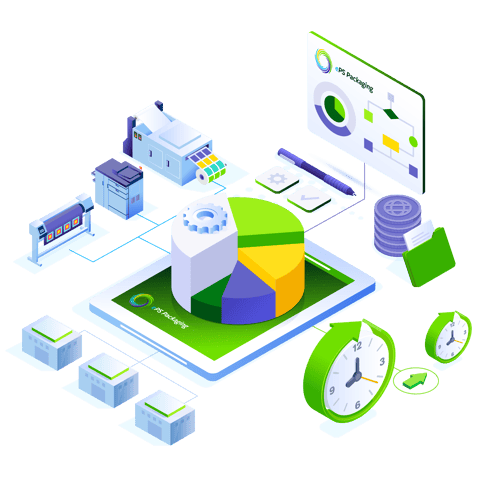
Limited production data?
Monitor run-order and machine status, sync data with your ERP system to unify data and streamline processes from across the plant floor.
Auto-Count® 4D (AC4D) is a cutting-edge production intelligence platform that optimizes equipment performance, helping you track costs and minimize downtime to run a more efficient operation.
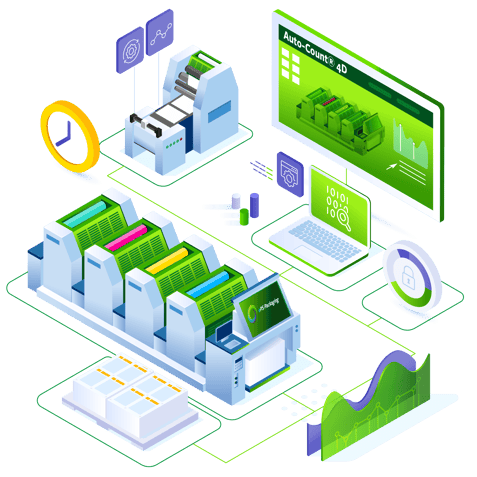
Time-consuming manual tasks?
Collaborate more effectively, by automating notifications of events such as: estimated approvals, product quality defects, low levels of raw materials…
Leverage tools to create event-based rules to direct the automation engine to execute a wide range of actions, minimizing touchpoints helping reduce or eliminate friction.
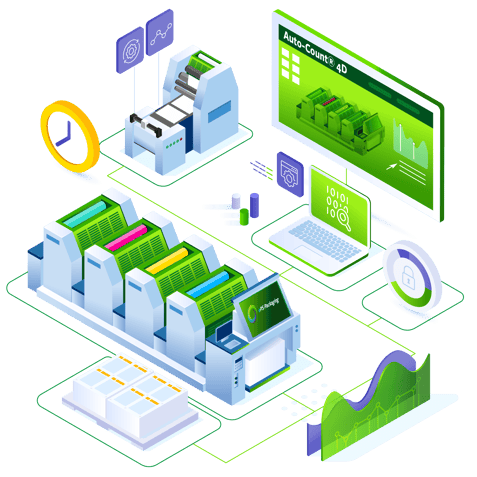
Frequently Asked Questions
What is a MES Application?
MES Applications are comprehensive software tools designed to monitor, track, document, and control the manufacturing process in real-time.
They act as the link between the production floor and enterprise resource planning (ERP), giving decision makers access to data to ensure that manufacturing operations are efficient and effective.
MES applications are also useful in heavily regulated industries, such as flexible packaging; by offering traceability and documentation features. This facilitates audits and improves quality control, helping to avoid costly compliance violations, but also importantly, builds trust with consumers and regulatory bodies.
MES vs. Other Industrial Systems: What are the Key Differences?
Enterprise Resource Planning (ERP)
While MES and ERP (Enterprise Resource Planning) systems both aim to improve business efficiency, they operate at different levels. For example, a none packaging specific ERP might focus on broader business processes, such as finance, HR, and supply chain management, whereas MES is specifically targeted at the production floor.
MES applications can connect with existing ERP systems to ensure a seamless data flow between production and business operations.
Additionally, MES interacts with IoT devices and PLCs (Programmable Logic Controllers) to gather real-time data from the shop floor. In the context of smart manufacturing and Industry 4.0 and 5.0, MES plays a pivotal role by integrating advanced technologies and enabling a more connected and intelligent manufacturing environment. Consider MES's as the glue between your factory and the information systems.
Manufacturing Estimating Software
Manufacturing Estimating Software (MES) shares the same acronym but operates in the field of cost estimation. To clarify, this software is specifically designed to simplify the calculation of costs and resources needed for manufacturing projects. It allows manufacturers to precisely forecast expenses for materials, labor, overhead, and production time, leading to faster and more accurate estimates. This topic is not covered in this article, but you can find out more on our article: on Improving Estimating Efficiency with Manufacturing Estimating Software
What are the key benefits of implementing an MES in packaging operations?
Implementing an MES application can lead to significant improvements in OPEX and COGS.
A recent report found that approximately 47% of companies worldwide utilize an ERP application, with the major players being well known companies like SAP, Oracle, Salesforce, NetSuite, and Acumatica.
Packaging-specific enhancements to these generic ERPs can improve scheduling, data collection, and offer real-time insights into plant operations.
Depending on functions, these MES applications can be implemented for a few thousand dollars per machine. They are flexible and versatile systems that are easy to integrate easily to existing ERP systems while cutting costs and time with tailored packaging technology solutions.
For example, some ERPs often rely on various scheduling and data systems from different providers, leading to potential integration challenges; while packaging specific solutions can provide a unified API and business object definitions, ensuring minimal integration effort and consistent product performance.
- Enhanced quality control: With real-time transmission of quality control data, companies using an MES can promptly stop production when issues are detected. This minimizes waste, scrap, excess production, and rework.
- Boosted uptime: An MES creates realistic production schedules by effectively balancing personnel, materials, and equipment resources. It synchronizes scheduling and maintenance to optimize product flow and asset utilization, thereby increasing uptime and enhancing overall equipment effectiveness (OEE).
- Lowered inventory: A manufacturing execution system keeps inventory records current with new production, scrap, and nonconforming materials, ensuring that purchasing, shipping, and scheduling departments are always aware of available materials. This reduces the need for just-in-case inventory and work-in-progress (WIP) inventory, leading to cost savings in manufacturing, transportation, storage, and inventory management.
- Digital shop floor: Removing paperwork reduces the likelihood of human error and ensures that data from the shop floor is instantly accessible to decision-makers across all integrated systems.
- Enhanced product tracking and genealogy: MES monitor the entire production cycle from start to finish, linking final parts or batches with their corresponding manufacturing data. This information supports improved regulatory compliance for manufacturers required to adhere to government or industry standards.
-
Improved Labor Productivity – MES track employee performance, automate data collection, and optimize workforce allocation, reducing idle time and improving efficiency.
-
Faster Time-to-Market – By streamlining production processes and minimizing delays, MES helps manufacturers bring new products to market more quickly.
-
Energy Efficiency – MES solutions can monitor energy consumption in real-time, helping manufacturers reduce waste and lower operational costs.
-
Regulatory and Compliance Support – Beyond product tracking, MES ensures adherence to industry regulations by maintaining accurate, auditable records for certifications and inspections.
-
Better Cost Control – With improved resource allocation, waste reduction, and automated tracking, MES helps manufacturers control costs more effectively.
-
Seamless Integration with ERP & Other Systems – MES bridges the gap between the shop floor and enterprise-level systems, ensuring accurate data flow for better decision-making.
-
Increased Flexibility & Responsiveness – MES enables quick adjustments to production schedules in response to demand changes, supply chain disruptions, or unexpected equipment failures.
Can an MES integrate with existing ERP systems?
Yes. Modern MES platforms are designed for interoperability.
They exchange production data with ERP systems to ensure consistency between planning and execution.
Integration allows for better alignment of inventory, production scheduling, and order tracking - eliminating silos and manual duplication.
Is an MES suitable for small to medium-sized packaging companies?
Yes. Scalable MES solutions that match the needs and budgets of SMEs are available. These systems can start with core features (e.g., scheduling, production order tracking, quality management) and expand over time.
Many SMEs find MES essential for leveling the playing field, improving performance, and winning business through better service and reliability.
What should be considered when selecting an MES for packaging operations?
Selecting the right vendor for MES implementation can effectively negate many of the challenges typically associated with these systems. By choosing a vendor with a proven track record, businesses can ensure compatibility and seamless data flow, minimizing integration issues.
It's especially important is to work with MES vendors that know your business and have a track record with your processes and machines.
Training and user adoption are critical factors that can determine the success of an MES implementation. Employees need to be adequately trained to use the new system effectively, and there must be a clear change management strategy to encourage user adoption and acceptance.
- Packaging-Specific Functionality: Look for features designed for web handling, roll tracking, print inspection, die cutting, gluing, etc.
- Configurability: Can the system adapt to your machines, workflows, and business rules?
- Ease of Use: A modern, intuitive interface reduces training and boosts adoption.
- Data Accessibility: Can users access performance and traceability data easily?
- Integration: Ensure compatibility with your ERP, prepress, and quality systems.
- Vendor Expertise: Choose a provider with experience in packaging and proven customer success.
How long does it typically take to implement an MES in packaging operations?
Implementation time depends on operation size, existing infrastructure, and deployment scope.
A phased approach, starting with core features, can often be implemented in 3–6 months.
Larger or more customized deployments may take 6–12 months, but this allows for better alignment with change management and user training.
What types of packaging production processes does an MES support?
MES platforms can support various packaging processes, including extrusion, printing (flexo, digital, offset), laminating, slitting, die-cutting, folding, gluing, and converting.
MES tracks each process's machine status, job performance, waste, and quality, enabling complete visibility and control.
Can an MES help with sustainability goals in packaging?
Yes. MES helps reduce waste, energy consumption, and overproduction by optimizing production runs and tracking resource usage.
Data captured by the MES can support carbon footprint reporting, waste audits, and sustainability certifications. It enables proactive improvements that align with circular economy goals.
How does MES improve traceability and compliance in packaging?
MES provides full traceability of materials, machine settings, operator actions, and product batches.
This is essential for meeting customer-specific requirements, food safety regulations (e.g., BRCGS, FDA), and certifications. It simplifies audits and ensures you can pinpoint root causes quickly if issues arise.
Can MES help manage short runs and high product variation?
Absolutely. MES is ideal for managing complexity in packaging operations with frequent changeovers, customized jobs, or high SKU counts.
It automates job setup, guides operators through changeovers, and helps balance throughput with flexibility - which is essential in today’s fast-moving consumer market.
Does MES support remote or multi-site packaging operations?
Yes. Cloud-enabled or centralized MES platforms allow companies to monitor and manage production across multiple locations.
Standardized processes and shared data models improve consistency, benchmarking, and resource allocation across sites.
What Are The Emerging Trends Influencing MES?
The global MES market is projected to grow to US$41.78 billion by 2032. This growth is being driven by an increase in the use of industrial automation in process and discrete industries, the growing need for regulatory compliance, and the low deployment cost of manufacturing execution systems.
The future of MES is being shaped by advancements in AI and machine learning, which are enhancing the capabilities of these systems. AI-powered MES can predict maintenance needs, optimize production schedules, and improve defect detection.
Cloud and SaaS-based MES solutions are becoming increasingly popular, offering flexibility and ease of deployment. As we move into the era of Industry 5.0, MES will continue to evolve, integrating more sophisticated technologies and focusing on human-centric manufacturing. These trends indicate that MES will remain a critical component of modern manufacturing, driving innovation and efficiency.