CL&D Graphics
Streamlining operations and boosting
efficiency with Radius
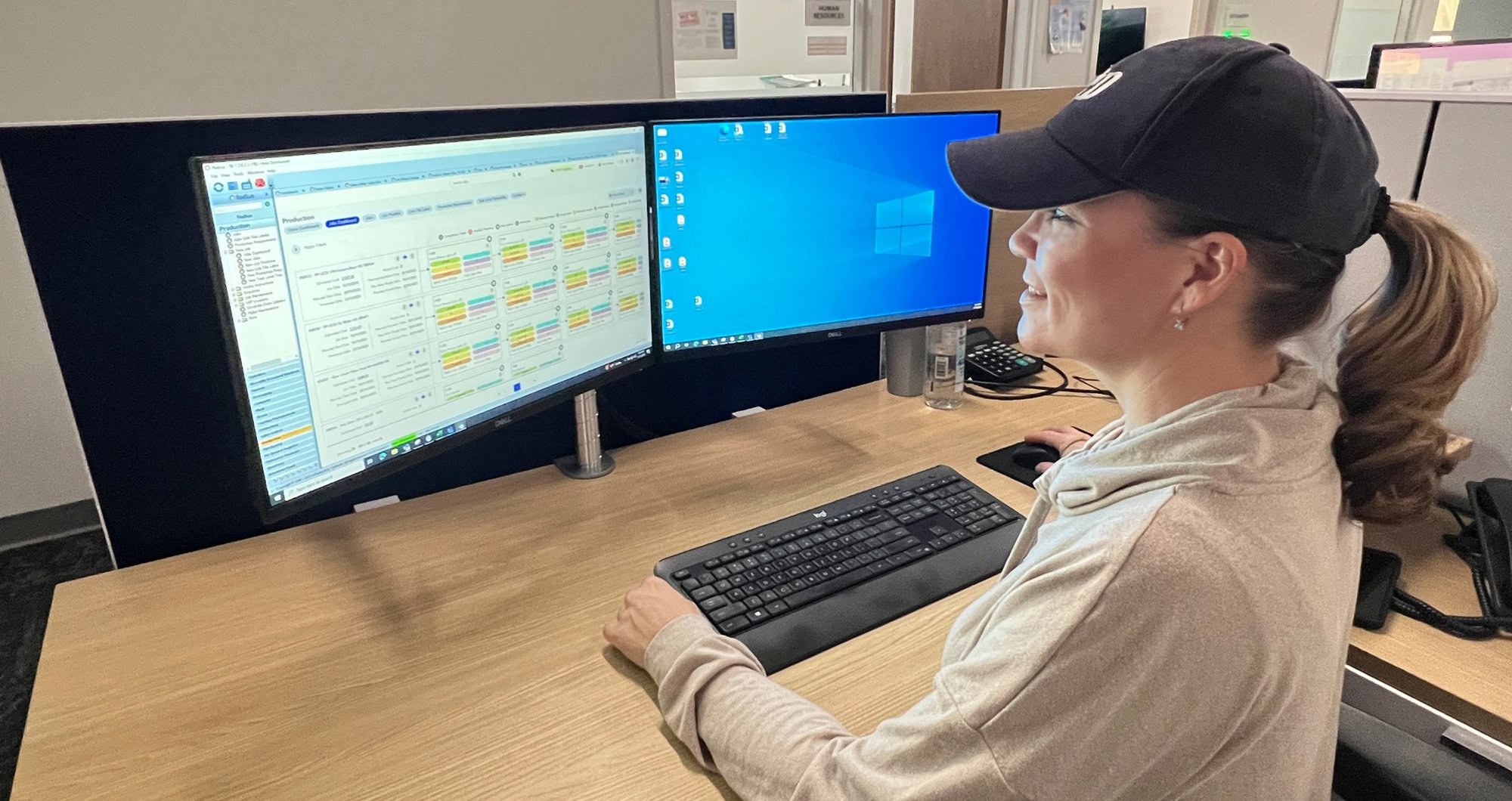
About the company
CL&D Graphics, an established leader in the packaging industry, forms a pivotal part of the ProMach Group due to its innovative and comprehensive packaging solutions that have been shaping the consumer packaged goods (CPG) landscape for over 40 years.
Located in Hartland, Wisconsin, CL&D—with a team of 280 employees—effectively utilizes its four facilities to provide an array of services, from roll-fed film and pressure-sensitive labels to shrink sleeves and pre-printed thermoform solutions. As part of the ProMach Group, a conglomerate renowned for its comprehensive packaging and processing solutions, CL&D rounds out the group’s offering by providing flexible packaging converting.
Delivering superior quality packaging by driving innovation and elevating client brands through its flexographic and digital printing services and providing solutions across various sectors, including food, beverage, personal care, and nutraceuticals.
In 2014, following considerable research, CL&D recognized the need for a more streamlined system to manage their entire business and replace multiple software solutions that lacked integration. As a result, they decided to invest in a comprehensive solution that would encompass all aspects of their operations.
One of CL&D’s key market advantages lies in its unwavering commitment to customer satisfaction. The company strives to deliver high-quality products with quick turnaround times. Therefore, the primary requirement for the new system was a swift implementation without disrupting ongoing production and the quickest ROI time to value.
After an extensive search, CL&D chose ePS Radius® ERP from eProductivity Software (ePS), an agile and robust platform tailored specifically for the packaging industry and dedicated tools for Flexibles. ePS successfully delivered CL&D’s implementation project minimizing significant downtime or disruption to the business.
“Thanks to the ePS team, the implementation process went remarkably smoothly given the scale of the project. We were able to keep our plants operational throughout, which was truly remarkable.”
Janell Held, Purchasing Manager
CL&D
The challenge
CL&D recognized the need for a more streamlined system to manage their entire business and replace multiple software solutions that lacked integration.
Key benefits
Streamlining operations and boosting efficiency with Radius
Janell explains: “Radius has brought structure and organization to our business, and now we simply add the necessary details and numbers to make it more effective. What’s great about Radius is that it helps us understand our business better and run it successfully. When we went live with the new ERP system, the ePS team was incredibly helpful. They spent a lot of time with us and helped us understand the interfaces, the logic, and the workflows.
However, when it comes to learning something new, embracing it, practicing, and discovering the nuances is the easiest way to gain the necessary knowledge. Thankfully, in the case of Radius, the system is designed to be intuitive and forgiving, allowing users to navigate through the platform which makes the learning process easy.”
Jason Einsel, Database Administrator at CL&D adds, “If users want to learn the Radius system on their own, it’s doable. Using Radius daily has provided us with a wealth of knowledge, and this is where the real excitement begins. Radius is an incredibly logical program, offering consistency across all its modules, which greatly aids in user experience.
A prime example of this are the Sales Order and Purchase Order modules, which are essentially mirror images of each other, allowing for a seamless flow from the user’s perspective.
“We chose Radius because it’s a best-in-class, out-of-the-box solution for packaging. It’s also highly customizable, allowing us to tailor it to our specific needs and run our packaging business exactly the way we want.”
Janell Held, Purchasing Manager
CL&D
Phenomenal traceability capabilities with ASNs and Radius inventory features
As a trusted supplier to the nutraceutical industry, CL&D is dedicated to upholding numerous regulations and industry standards imposed by the FDA.
For the company, ensuring compliance is of utmost importance, especially when it comes to supply traceability. The challenge lies in the fact that many suppliers provide Advanced Shipping Notices (ASNs) in various formats. Despite this hurdle, CL&D capitalizes on the benefits of ASNs and inventory features in Radius, which prove to be invaluable in terms of timesaving and enhanced traceability.
Accessing information from different areas of the system empowers CL&D to make well informed decisions.
For instance, users can instantly review the inventory references used and the corresponding jobs they were linked to. This level of transparency is particularly valuable in situations where quality issues arise with a specific part of the supply delivery. By utilizing ASNs and the Radius inventory reference, CL&D can effortlessly identify which supplies meet the quality standards, as well as determine which jobs utilized the same material from the corresponding purchase order. Such comprehensive insight ensures efficient quality control and enhances overall supply management.
Packaging Suite
The Packaging Suite from eProductivity Software (ePS) is a comprehensive and purpose-built solution for all sectors of the packaging industry, including folding carton, tag and label, flexible packaging, and more. It offers tools for cost estimation, scheduling, real-time shop floor data, and eCommerce--all aimed at optimizing operations and enhancing efficiency.

Transforming waste management and inventory optimization
Before the implementation of Radius, the job-based system at CL&D lacked important functionalities like waste management. As a result, there was no visibility into waste efficiency, leaving the company in the dark about the amount of waste and resulting costs for each job produced.
This lack of data hindered the ability to take appropriate action and understand where the best areas to improve and optimize would be. However, following the installation of Radius ERP, the company can understand and measure the amount of waste generated by each job and make informed decisions to minimize waste and improve efficiency.
Moreover, Radius has also changed CL&D’s approach to inventory management, providing full visibility across the warehouse and ensuring timely stock availability. The Free Stock Planning feature ensures everything the company needs is readily available, eliminating delays and shortages.
Since Raw material costs continue to be the largest cost component to produce a package, the enhanced control over inventory has streamlined operations and allowed the company to reduce the cost of waste effectively.
“Now, CL&D can discuss waste management, inventory optimization, and other aspects of the business across all departments, setting ambitious goals for the future. With Radius at the center of our company, CL&D is equipped to take on new challenges and drive continuous improvement across its operations.”
Janell Held, Purchasing Manager
CL&D