Dunapack
Dunapack Packaging's accelerated journey to higher corrugator speeds and improved board quality with Escada
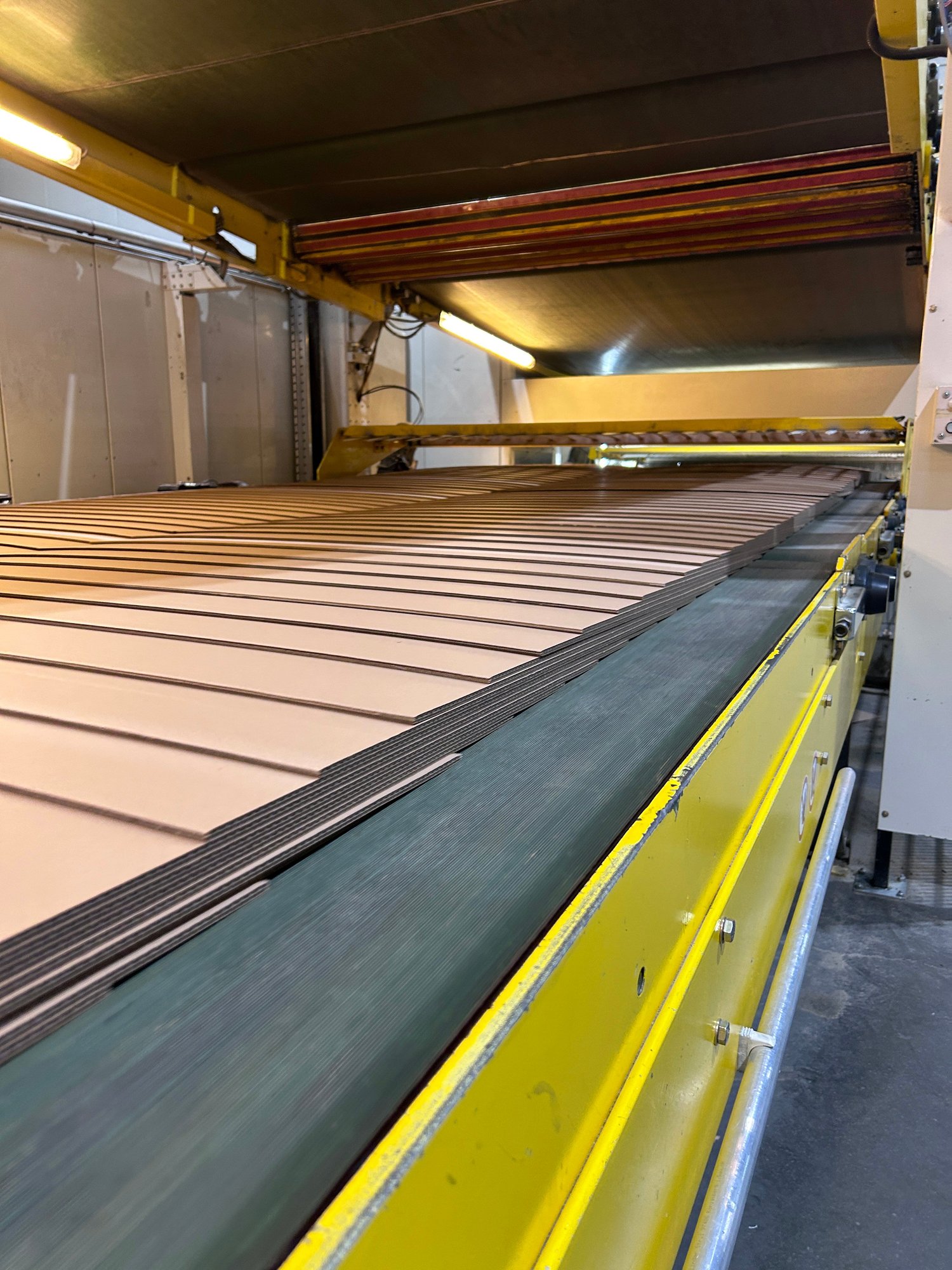
About the company
Dunapack Packaging, a member of the Austrian Prinzhorn Group, is deeply involved in the corrugated industry, covering the entire value chain, including recycling, paper production, and converting corrugated board boxes, executed at a high-quality level.
Exceeding 6000 employees across 12 countries and 24 plants, Dunapack Packaging is the regional market leader in Central and Eastern Europe, meeting customers’ highest packaging requirements and delivering innovative and competitive packaging solutions.
Sven Warsoenke, Operations Director at Dunapack Packaging, Spremberg, Germany, oversees the production area, including the corrugator, converting machines, maintenance, purchasing, planning, and logistics. With 11 years of experience in the packaging industry, Sven has been with Dunapack for almost four years, focusing on the corrugated business.
The Spremberg plant, built in 2005 and located next to the Hamburger Rieger paper mill, is a fully integrated corrugated plant serving various industries.
The challenge
Dunapack had a growing demand from their market and were looking for opportunities to increase the output of their corrugator.
Dunapack reached the decision that they also needed to implement a process control system: controlling warp, controlling temperature, controlling all the things that influence the quality of the board.
Key benefits
“Our corrugator had been in operation for 18 years, but we began to see a decline in performance and couldn’t establish a clear understanding of the cause. Initially, we met with our OEM, and we discussed implementing a target speed system, but at a certain point, we concluded that a target speed system on its own would not solve the problem as we also had issues with the stability and the quality of our product.”
Sven Warsoenke
Operations Director
The solution
The decision to adopt eProductivity Software’s Escada corrugator process control was influenced by positive experiences shared by Sven’s colleagues at sister plants across Europe, who had all experienced successful implementations of Escada.
The decision was made easier as Sven comments on how the ePS Escada team engaged with him on the project:
“We were treated as an important customer, and the atmosphere within the team was always positive, friendly, and, most importantly, calm. The Escada team was focused on results and facts; it never felt like you were dealing with a salesperson, more of a consultative approach to understanding our business challenges and having an open discussion on solutions. It was very service and goal-oriented, which we appreciated.”
"Our conversations with the Escada team, the competitive commercials, and feedback from wider teams within the group gave us the confidence to proceed. Of course, there is always a certain level of risk associated with any investment project, but from each step and engagement in the process, the level of risk decreased.”
“Moving to a new non-OEM supplier can be quite a mental jump – we have a good relationship with BHS, and while they helped us explore an initial solution, we recognized that it wouldn’t address all our concerns. As a business, we take investments seriously, scrutinizing them to follow a strict rule of return."
Dunapack proceeded with Escada’s Profile (closed-loop process control), Intelligent Speed Control (automatic speed control), and Next Gen Clarity solutions (business intelligence and reporting).
Onboarding and go-live
“The implementation process held challenges that were more internal than with Escada – as you can imagine, with a company like ours, resources are narrow as people already have a lot of work to do. Any new projects take time, and you have to account for the team's training, which takes them away from their usual duties. This is an area where the Escada team shone as a guiding light to help navigate us through the process."
"We were equipped with documentation and briefing meetings before the go-live. The mechanical and electrical work was commissioned in preparation for the Escada team to complete the final parts of the installation. Everything went smoothly; we had some minor issues in the first week, but the installation team was on hand to resolve them quickly, further cementing our decision that Escada was the right team and choice for us."
“Our operators had a great training experience from Escada – the trainer was extremely knowledgeable and committed to the project, ensuring our team would succeed. If we had questions, they were answered thoroughly, and we were (and continue to be) provided with training guides and videos to assist us. This is a big tick from our perspective as even though we are investing in technology, the people are at the heart of our business, and ensuring that they are equipped with the right tools and support enables them to succeed.”
The results
The collaboration with the Escada team was marked by a focus on results and a service-oriented mindset. Despite minor initial post-installation issues, the team's dedication and swift problem-solving demonstrated a commitment to Dunapack's success.
“The onboarding and go-live went smoothly; now we were in the production phase with testing and results under scrutiny. We were interested in understanding the feedback from the operators and how their days had changed since Escada. You can imagine that when you install a system like this, the doubts and prejudice of the team are there; they don’t trust the system as they’ve been running the corrugator for 17 years without any system. Previously, the operators trusted their gut feelings – there were no temperature sensors or controls; they were running the corrugator with their knowledge and pride in what they were doing. There’s a fear that with new technology, it could prove that they were doing something wrong – this did not happen; it turned out that the biggest part of their work was done excellently, and they were more than happy to accept the inputs from the Escada system as it only further improved the work they were doing.”
“We began with Escada Profile for process control; the added value this gave the team was immense. For the first time in 17 years, they could now see temperatures and pressures on the corrugator, whereas previously, they would look at the board to see what the machine was doing and then decide what to do with the temperature and pressure. Having real data helped convince them that this was a great solution, and they were eager to experience more. We saw that we could decrease the single-facer steam pressure for various grades; we started with 12 bars, and now we are at 10. While I don’t have any figures relating to the consumption, this reduction in pressure will no doubt have an impact on energy usage.”
“The second phase was to implement Intelligent Speed Control. This was more challenging than Profile for the operators to accept initially as they are used to running an E flute at a certain speed, a B flute at this speed, and so on - it put pressure on the team. Still, they now accept it, and the system is running in automatic mode and running well for us. We went from a starting point of 213 meters per minute to 228 meters per minute, an increase of 7%. This, coupled with the decreased downtime, is quite significant.”
Commenting on the onboarding of new staff, Sven said: “The biggest problems we had with training new staff were on the single-facer and the double-backer – these two machines posed a challenge, but with Escada, the knowledge sharing among the team, coupled with the training materials has helped to support new operators and with Profile for warp control, it’s made it easier for them to understand which parameters influence the quality of the board – it’s all made a positive impact.”
-
Higher production speed
A significant increase in corrugator speed was achieved.
-
Steam consumption improvement
Notable reduction in single-facer steam pressure from 12 bars to 10 bars, anticipating positive impacts on steam consumption.
-
Quality enhancement
Significant improvement in board quality, addressing issues like warp and overall board moisture level. Colleagues, stakeholders, and customers have acknowledged this.
-
Reduced waste
As a result of improved board quality, less waste has been produced.
-
Return on investment (ROI)
While specific ROI figures are pending, there is confidence in Escada delivering as promised, with a budget anticipating a payback period of less than a year.
-
Impact on staff turnover and training
Escada simplified training for new operators, enhancing their understanding of parameters influencing board quality.
Future plans and acknowledgment
Dunapack recognizes the potential for Escada in future investments, especially in addressing challenges related to quality, corrugator performance, waste reduction, and energy efficiency. The positive collaboration with the Escada team has set the stage for potential future expansions within the Prinzhorn Group.
“ESG (Environmental, Social, and Governance) will become a big issue in the coming years; we [Dunapack] are putting a lot of effort into this topic and will work with the Escada team to explore capabilities to align with our energy management and sustainability goals.”
“The three main concerns are quality, resources, and energy. We must continuously improve board quality; this is where Escada helps support the performance of the corrugator. Resources – the need to hire and retain people and ensure they are equipped with the tools to succeed, and finally, energy – reducing energy consumption and waste to help our planet. I’m quite convinced that Escada as a system and the people supporting it will be key in helping us to deliver on all three points.”
An appreciation for the ePS Escada team and collaboration
“I am extremely grateful for the commitment and service level of the Escada team. The positive teamwork and collaboration encourage continued support. It’s uncommon in the industry to have such a collaborative experience working with a supplier like this. It is a perfect combination of great teamwork, technology, and results, and I’m sure it is one of the key reasons other plants in the group are also investing in Escada.”
Sven Warsoenke, Dunapack
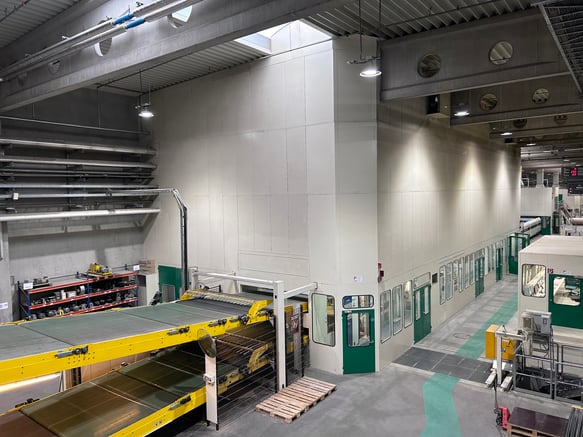