Kendall Packaging
Kendall
Packaging on the Path to Greater
Efficiency
With different departments each tracking and collecting information independently, Kendall Packaging needed a software solution that would allow it to set measurable goals and develop process improvements.
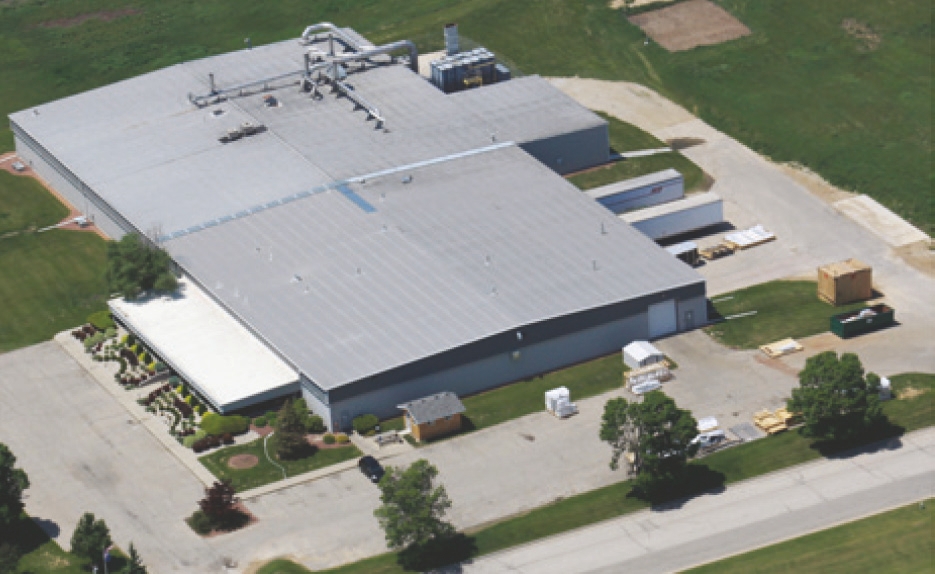
About the company
Kendall Packaging Corporation, headquartered in Mequon, Wisconsin, is a preferred flexible packaging converter offering its customers rollstock, pre-made bags, stand-up pouches, shaped pouches, striped metalized film, and high-performance barrier film.
Since 1948, Kendall has had a reputation for providing superior customer service, which it has earned from its state-of-the-art equipment, systems, and personnel. Its streamlined workflows give it the ability to consistently accommodate demanding delivery schedules and short lead times - the epitome of today’s customer needs.
The challenge
Kendall Packaging was losing too much time in the creation and adaptation of reports.
With different departments collecting and reporting information independently, it was difficult to identify deficiencies and track progress.
Key benefits
“So much time was being spent on the creation and adaptation to reports themselves. No matter how much we tweaked them, we were still looking at pages of static numbers.”
Russ Schneider,
VP Quality & Engineering Kendall Packaging
Solution
Departments were collecting and reporting information independently. This made it difficult for management to identify deficiencies and track progress on a corporate level. Too much effort was wasted defining reports that didn’t support a proactive decision-making process.
Kendall Packaging sought the flexibility and speed of a dynamic information tool. “Our hope was that a business intelligence tool would make data more accessible to the right people and that they could use it to solve problems,” says Schneider.
“We could see what was on the reports, but as far as ‘what-ifs,’ people couldn’t really go in to change the report to give them different answers. That was our expectation of a new tool.”
After one demonstration of the ePS Radius Business Intelligence (BI) tool, Kendall Packaging knew it was going to be the solution it needed. “It basically sold itself,” says Schneider.
Its user-defined nature and flexibility for manipulation made it a tool that would work for anyone at Kendall.
Whether someone in production needed to find out how to improve the use of a press, or the CEO needed to analyze sales trends, BI was going to work.
As one of the first users of the BI tool, Schneider knew there was likely going to be a learning curve, as is the case with any software.
“BI is very useful right out of the box,” says Schneider. “But, to get the most out of the system, we worked closely with the team at ePS Radius to tailor the solution to the specific needs of our business.”
Any company making an investment in new software should make sure the technology is working well for others as well.
Schneider says, “We talked to another ePS Radius user who had implemented BI and they had done a great job at putting things in place and making it a daily tool for their executives. It helped to hear their success story.”
Packaging Suite
ePS offers a robust portfolio of highly flexible, modular packaging software solutions designed specifi cally for label-making, folding carton, flexible packaging, and corrugated packaging industries. Our packaging solutions drive profitability, reduce the cost of sales and manufacturing, and empower successful transformation.

Results
With improved visibility of manufacturing metrics, Kendall has been able to set measurable goals and develop process improvement teams that track progress.
Schneider says, “With the click of a button, we can drill down by work center, product type or customer. We can easily combine these filter criteria to find problem spots and sort through the data to find areas where we should focus more of our efforts.”
With BI, Kendall has been able to optimize press speeds, minimize downtime and reduce make-ready times on its presses.
While many companies without Business Intelligence struggle to make information available between departments in a single building, Kendall Packaging has been able to leverage information between each of its three locations. Schneider says, “Being a multi-plant organization, BI definitely helps bring all of our data together.
It has increased the visibility of each plant’s performance - we can look at data and make quick decisions because it is all right there in front of us.”
Finally, Schneider admits that while his company counts on an internal resource to set up new BI reports, sometimes a reporting requirement may be outside their expertise. That is when working with a trusted partner like ePS comes in handy.
The BI product experts work on the same team as the ePS Radius ERP experts and their shared knowledge contributes to the strength of the BI tool.
“If there are reports we want to create that are too complex for us, we know we can count on ePS to be there to help us get where we need to be. We know the ePS employees well and they are great to work with,” says Schneider.
“The analysis that used to take us half a day to get ready now takes us five minutes.”
Russ Schneider,
VP Quality & Engineering Kendall Packaging