In a high-speed corrugated environment, you’re surrounded by moving targets - paper quality, heat levels, tension, speed, glue mix, splice timing. When something goes wrong, the instinct is to act...
Mastering Backwards and Forwards Planning in Corrugated Manufacturing
Corrugated manufacturing is a complex process that involves various stages, from raw material sourcing to final product delivery.
Manufacturers often rely on effective planning techniques to streamline operations and optimize efficiency. Two approaches commonly employed in the industry are backwards planning and forwards planning, also known as push vs pull planning.
In this blog post, we will explore these planning methods in the context of corrugated manufacturing and highlight their benefits for businesses in the industry.
Contents
What is backwards (pull) planning?
Backwards planning, as the name suggests, involves working backwards from the desired end result to determine the necessary steps to achieve it. In the box plant context, the conversion (customer box orders) will drive the demand for the sheets. This methodology will create, in turn, the demand for sheets, thus calibrating, in theory, the perfect balance. As backwards planning starts with customer box order demand, aside from reducing WIP (Work In Progress) levels of sheets, it will also prioritize the timely delivery of finished products.
Here's how it works:
-
Customer demand analysis: Manufacturers begin by analyzing customer demand for specific box orders, considering factors like order volume, delivery deadlines, and product specifications.
-
Production scheduling: Based on the demand analysis, manufacturers establish a production schedule that outlines the necessary quantities and deadlines for each order. This schedule considers lead times, machine capabilities, and available resources and drives the demand for sheets from the corrugator.
-
Material obtainment: With the production schedule in place, manufacturers can accurately determine the required sheets of board and other materials, such as adhesives and inks. Backwards planning enables corrugated manufacturers to optimize inventory levels and reduce the risk of running out of stock or having excessive inventory.
-
Process optimization: Once the raw materials are secured, manufacturers plan and optimize the converting machine processes (printing, cutting, and assembling). This process involves assessing the production capacity, machine capabilities, and labor availability to ensure smooth operations.
Quality control and packaging: Backwards planning incorporates quality control measures throughout the manufacturing process. The final step involves packaging the corrugated products so they are ready for shipment to the customers.
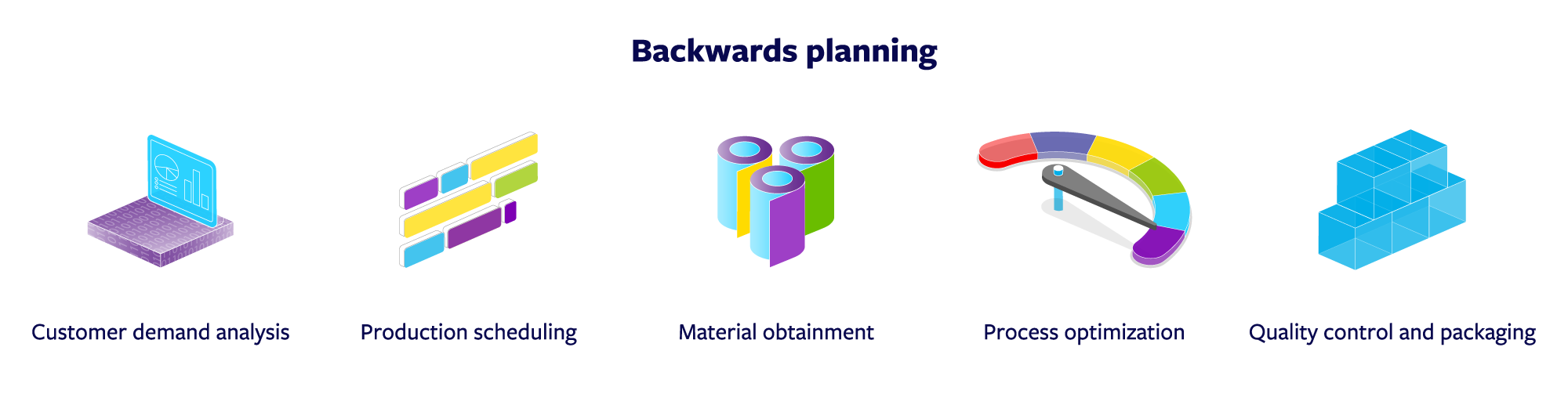
What are the benefits of backwards planning
Backwards planning offers several advantages in corrugated manufacturing:
- Enhanced customer satisfaction: By aligning production with customer demand, backwards planning ensures on-time delivery and meets customer expectations consistently.
- Efficient resource utilization: Manufacturers can balance roll stock, corrugated sheet production, and machine time with their converting demand, thus minimizing WIP levels, working capital, overrun waste, and reducing inventory carrying costs.
- Improved Production Efficiency: Backwards planning allows manufacturers to avoid WIP build-up with space constraints, avoid bottlenecks, streamline processes, and maximize throughput while reducing lead times.
What is forwards (push) planning?
While backwards planning focuses on meeting customer demand by maximizing the utilization of raw materials, machine time and labor, forwards planning emphasizes corrugator efficiency and pushes WIP from the corrugator through the converting processes.
Here's how it works in corrugated manufacturing:
- Order Selection: Orders are grouped by flute, board grade, and order due date time within each board grade.
- Corrugator Optimization: Orders are trimmed/scheduled to make the corrugator as efficient as possible; this generally means fewer flute and paper changes, maximizing web width while keeping side trim to a minimum. This is done with little consideration for the needs of the converting machines.
What are the benefits of forwards planning?
Forwards planning offers the following benefits in corrugated manufacturing:
- Reduced corrugator downtime: The corrugator has fewer changeovers in flutes and board grades and theoretically runs more efficiently.
- Larger order pools: With the focus on corrugator efficiency, larger pools of orders in the same board grade are typically grouped together.
- On-time deliveries: In the case of a sheet feeder, grouping orders is paramount to utilizing truck space while meeting customers' due date time requests.
- Forward planning is the “only way to go” for corrugated sheet-feeders.
Conclusion
Effective planning is paramount for success in the fast-paced world of corrugated manufacturing. In a box plant, the ideal planning philosophy combines backwards and forwards planning. By starting the planning cycle with backwards scheduling, you create the ideal group of orders to be corrugated that, in theory, when you forward plan, maximizes the efficiency of the converting machines given the order mix and availability of the machine.
Once the orders to be corrugated have been selected through the backward process, the orders are trimmed; if the results are outside the scheduling goals, further orders can be added or removed from the available pool. This enables the ideal schedule to be created while meeting the needs of the converting machines. Once the corrugator schedule is set, the forward plan is run using machine-specific rules considering available WIP stock and the timing of orders/sheets off the corrugator.
The flexibility of modules within the Corrugated Suite, like CorrPlan® (converting scheduling), and CorrTrim® (corrugator scheduling), is particularly beneficial to corrugated manufacturers, supporting both forwards and backwards scheduling abilities, facilitating efficient scheduling, allowing planners to create the lowest-cost production schedules, balancing inventory levels, and sequencing orders effectively.